Using GIS to Help Meet Lead Service Line Identification Requirements
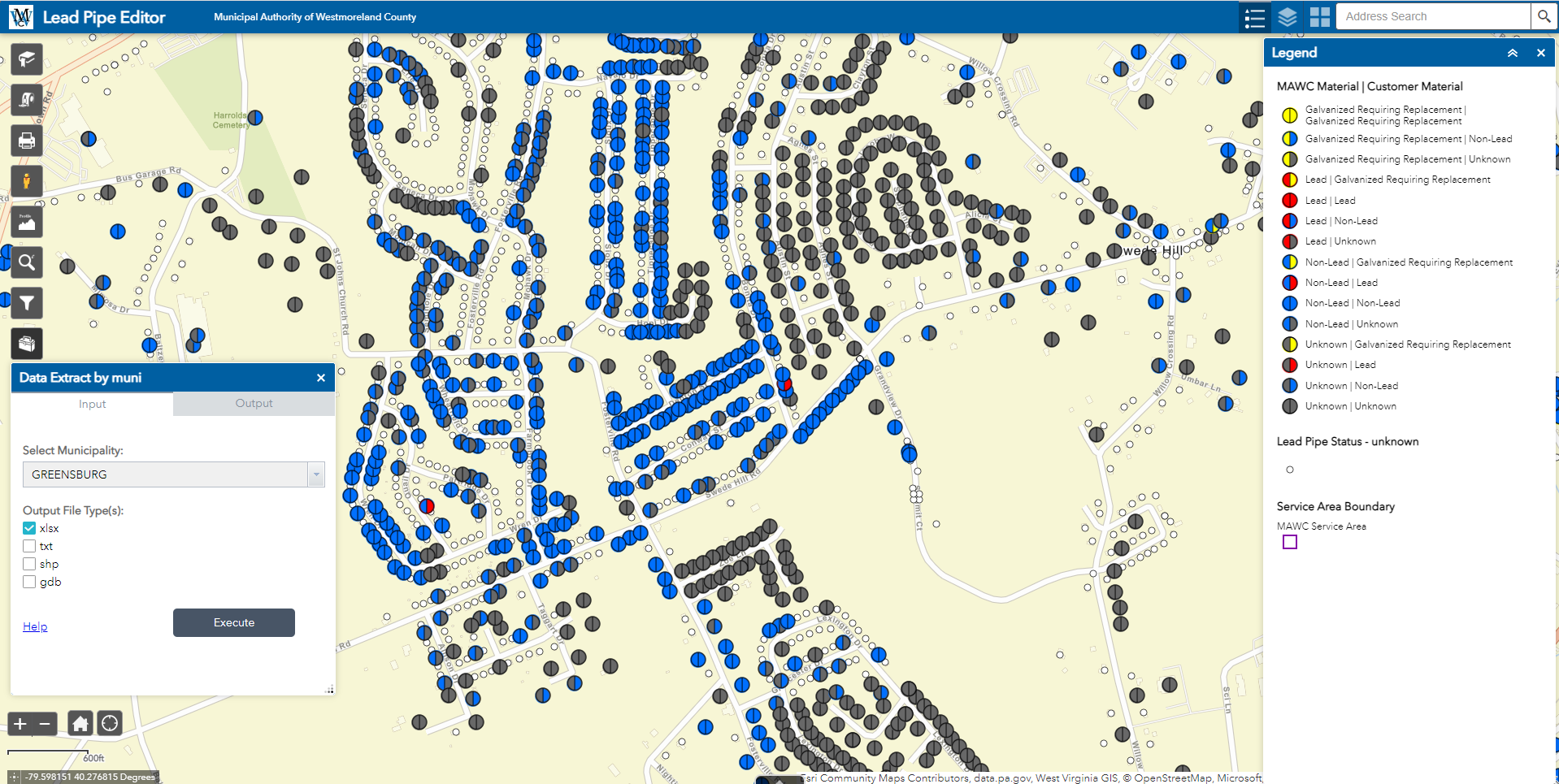
Lead exposure is a public health hazard. Even low levels of lead exposure can cause developmental effects in children and other serious health consequences for people of all ages.
In late 2021, the Environmental Protection Agency developed the Lead and Copper Rule Improvement regulation to protect citizens from exposure to lead in drinking water. The rule requires that all water system service line material inventories be submitted to their respective state by October 16, 2024. Additionally, all customers with lead service lines, galvanized service lines, or unknown service lines must be notified of their materials status within 30 days of completing the survey.
For authorities/municipalities that serve more than 50,000 customers, the inventory must be publicly accessible, ideally through a web map. Materials inventory, reporting, and notification are required for service lines owned by both the customers and the authorities/municipalities. These are the federal laws in place, but some states have passed laws that are more stringent than the federal requirements.
Using GIS to Help Meet Requirements
Authorities can use GIS to help meet lead service line identification requirements. For example, GIS is an ideal system to act as a central repository for storing the service line material information. It can easily be integrated with third-party datasets and allows for straightforward tracking, reporting, and analysis.
Building permit data—typically available through city/county offices—should be leveraged early in the service line material identification process. This data can usually be linked in GIS to available parcel data, and then the lead line inventory can be updated to “not lead” for any property built after January 1, 1987 (after which federal law banned lead line use in construction). Note that local laws should be checked to confirm if some companies were given an additional grace period to install lead lines.
Below are some other ways that EBA’s clients are using GIS for materials inventory, reporting, and notification.
- Tracking progress. Esri Dashboards enable users to clearly track progress of materials captured, lead line locations, and unknown material types to be investigated. Using out-of-the-box filter tools, web applications can be configured to view and filter service line materials on both the customer’s and authority’s service lines.
- Esri’s Field Maps. This application can be configured to capture service line material data when field crews perform routine maintenance. These easy-to-use forms can be configured with dropdown menus to standardize data inputs and auto-populate key information, such as server locations, addresses, and account numbers. Data captured in Field Maps update in the Esri data and associated dashboards in real-time.
- Public-facing maps. Web applications can be configured and hosted to meet the requirement of providing a service line material inventory to the public in an easy-to-view format. Customers can also verify their service line material and age of the associated infrastructure.
- Reporting and notification. Data can quickly be exported from GIS to spreadsheets that meet state reporting requirements. Additionally, a list of customers to be notified, including contact information, can be generated through data stored in GIS.
- Customer engagement. Esri’s Survey123 forms can be sent to customers with unknown service line materials and accessed through a QR code. The form includes easy-to-follow instructions on how to test and report for lead service lines. Data and pictures can be uploaded into a QC database for review prior to merging them with the live data.
- Python scripting. Scripts can be used to autogenerate status reports and data submittals. Data can be emailed directly to a predetermined list of people on scheduled dates. Scripts can also be used to help merge third-party datasets and QC databases.
GIS is an essential tool in all phases of the lead service line identification, tracking, and reporting process. Using the tools, applications, and processes listed above will not only help authorities meet their requirements, but ultimately help them identify lead service lines that need to be removed, which will support safe and clean drinking water for customers.
Joe DeLuca, GISP, is assistant vice president of EBA Engineering’s geospatial technologies and asset management division. He can be reached at 717.510.9873, joseph.deluca@ebaengineering.com, or on LinkedIn.