Water Asset Management 101
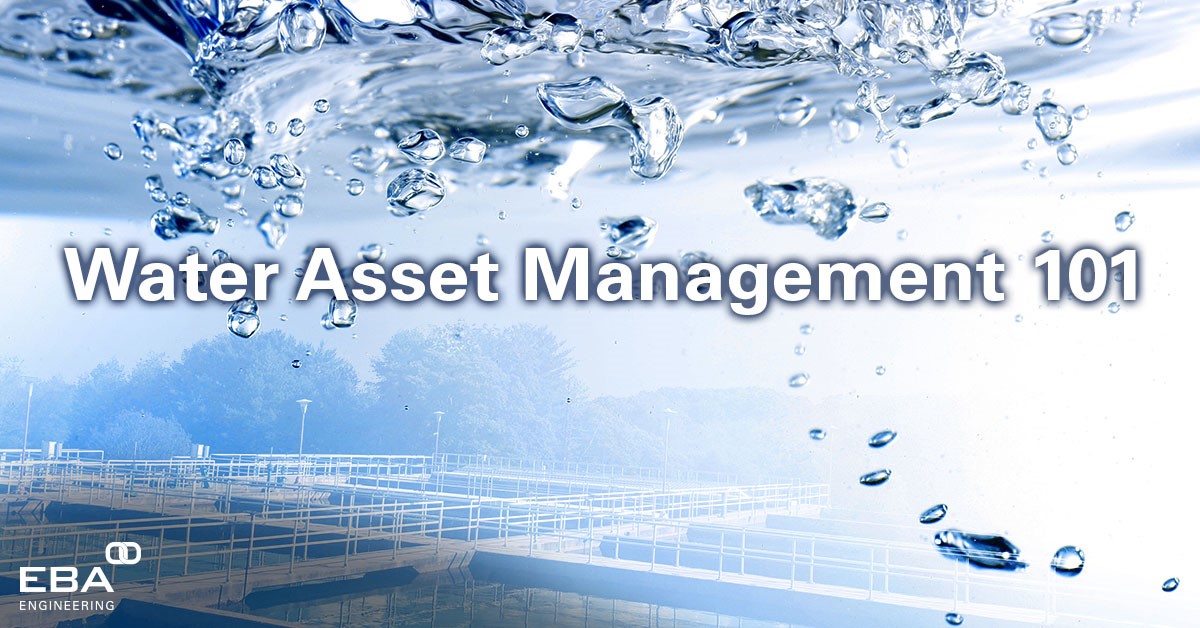
In my role as President and CEO of EBA Engineering, Inc., I regularly attend industry conferences and will discuss asset management with the utility managers I meet. During these conversations, water industry leaders will often share their issues and concerns with me, which always leads me to wonder how I can help them. What do utility managers need to know about asset management, and how can they leverage an asset management program to help them overcome their challenges?
I have been involved in the water industry for the last 35 years, focused primarily on planning, design, and asset management for water and wastewater systems. Water asset management is critical to delivering safe drinking water to our homes and businesses through conveyance pipelines, pumping stations, treatment plants, and other infrastructure. My work has ranged from large asset management programs for clients like DC Water, WSSC, and Baltimore City to smaller utilities. One way I have tried to answer these questions and help my clients—large or small—is through offering a human-centered training approach to some of the fundamentals of water asset management.
Why is water asset management important?
Think of the importance of asset management like the importance of managing our own bodies. We visit doctors annually to make sure we maintain our bodies and our health, especially as we age. Water infrastructure is really no different; it must be monitored and maintained regularly. Managers must ensure that their assets are in good working condition, because if they fail, organizations will face both human/environmental emergencies and big, unexpected costs.
Unfortunately, we do not need to look far for some sober warnings of what can happen when water assets fail. Here in the DC Metro area, for instance, many remember the 2008 water main break that turned River Road in Montgomery County into a virtual river, trapping motorists in water as high as 4 feet.
We want to make sure that all assets, systems, and infrastructure are more reliable and that citizens get the most out of their investment in infrastructure. The ultimate goal is to ensure safe, reliable drinking water for all citizens.
Why don’t utilities perform water asset management?
In my experience, many utility managers understand and are fundamentally invested in the importance of asset management, but they face similar issues in actually implementing an asset management program. I have surveyed a number of utility leaders nationally, and I found that they face several common challenges:
- Lack of mandate. When there is no state or federal requirement to perform asset management, it becomes a lower priority.
- Lack of financial resources. This comes as no surprise, as all utilities face the challenge of doing more with fewer resources.
- Lack of human resources. Small staffs are already responsible for maintaining hundreds of miles of pipeline infrastructure, pumping stations, and treatment plants. Retirements have also caused a loss in institutional knowledge.
- Fast-changing technology. Utilities may not have the most current tools and/or expertise to use them and upgrade their systems regularly.
- Lack of leadership or champion for asset management. Without the leadership of someone invested in asset management, it will likely not get done.
The COVID-19 pandemic has of course exacerbated these challenges as employees strive to maintain water systems from a distance.
How can we help utilities with water asset management?
Asset management is more than just keeping a bunch of spreadsheets; there really is a science behind it. Even the smallest utilities need an asset management program—a plan and a documented process for maintaining assets.
Industry experts can help utilities leverage the latest technology to track deterioration in their systems over time. Just as a body will deteriorate without care, a water system will deteriorate without maintenance. Water system deterioration and performance must be tracked annually to identify and address problems.
One way to track this deterioration is to benchmark historic data and compare it to current performance. Another method is to compare your system performance to other similar systems to identify areas for improvement. The overall intent is to extend asset life, improve life-cycle costs, and get the most value out of system delivery.
Water Asset Management 101 training
Knowing the many challenges that utility managers face, how do we support the importance of establishing an asset management program? To help utilities, in collaboration with the WaterCitizen Foundation, a non-profit dedicated to education the about water industry, we have created a 6-step, guided water education program that covers the main steps of developing an asset management plan. The 6 steps in this process include:
- Condition assessment. This step leads to understanding what your assets are, where they are, and what condition they are in.
- Criticality modeling. Using modeling techniques, the organization will determine how critical each asset is and the risk of each asset failing.
- Risk determination. Through this process, utilities determine the risk and likelihood of asset failure.
- Rehabilitation prioritization. Once a utility understands the risks, they can prioritize the rehabilitation process. No agency has the funds to do everything in one year, so this step identifies the issues that need to be addressed first and develops a long-term plan.
- Identify funding. It is important to consider any resources available, such as state and federal grants, to support the program efforts.
- Develop a capital improvement plan. The utility will need to develop a short- and long-term capital improvement plan (CIP) to spread their resources over the next 5–10 years to maximize the useful life of assets throughout the system.
For more information and to discuss your water asset management needs, please contact me at rizwan.siddiqi@ebaengineering.com.
Rizwan Siddiqi, PE, is President & CEO of EBA Engineering, Inc. He can be reached at 240.547.1125, rizwan.siddiqi@ebaengineering.com, or on LinkedIn.