Biomass to Energy Part One: Engineering the Future of Waste Processing
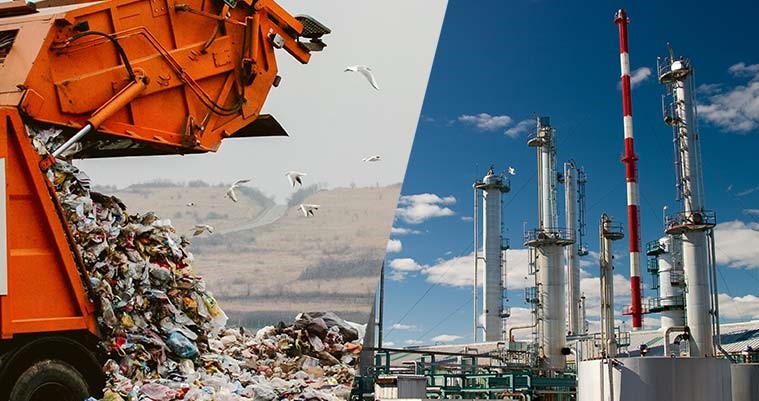
“Biomass to energy” is currently one of the fastest growing engineering fields in the U.S., and it really is as impressive as it sounds. Biomass to energy turns a “waste” into an energy-generating resource by either breaking it down to release gas or burning it—both of which create energy that can drive an engine generator, microturbine, fuel cell, and more.
This exciting new field has stemmed from sustainability programs, increasingly embraced by U.S. corporations and their suppliers, that seek to identify more environmentally benign ways to convert waste products into energy or fuel. Driven by the market demand for sustainability programs, new technologies have been developed to apply and use these wastes.
For example, “wood to biochar” is a new biomass to energy technology that is now being applied to large-scale projects in the U.S. The process converts waste wood such as telephone poles, railroad ties, or saw dust waste under zero oxygen conditions into a “biochar.”
Biochar is a carbon rich product that can enhance plant growth, be used for nutrient removal, or be used to produce carbon fiber materials. The wood-to-biochar conversion technology produces water vapor (and therefore has no air emissions) as it generates hydrogen gas from the zero-oxygen heating of the waste wood streams in a closed vessel at temperatures above 1100° C. The hydrogen gas can then be burned in a generator to make electricity. This process can also be used to generate diesel-type biofuel in a liquid state, which is more environmentally friendly and has a higher cetane (energy) rating than conventional diesel fuel.
This technology can even handle feed stocks like bamboo cuttings, tires, waste plastic, and wood from construction and demolition debris.
Biomass to energy technologies of the past
In the recent past, this arena was dominated by a few technologies like converting corn into ethanol, which is how 90 percent of our ethanol for gasoline is currently produced.
Until recently, large municipal incinerators were the most popular major biomass to energy systems being installed. These large-mass burn systems take all municipal trash/waste (with no separation) and burn it to make electricity by super heating water with the heat from combustion to drive steam turbines. Landfills were the last major arena of biomass to energy, as decomposition of municipal waste in landfills produces methane gas for energy.
Recently, however, recycling programs have removed high BTU wastes needed to generate electricity (like paper and plastic) from waste streams. In many cases, these incinerator operators are now purchasing wood chips to augment their waste stream just to ensure enough electricity generation to meet the facilities’ financial goals.
Large mass-burn systems are therefore not efficient and are being phased out due to high operating costs, poor environmental records, and poor return on investment.
Shifting the biomass to energy paradigm
Today, the paradigm of biomass to energy is shifting. New technologies can now take the same waste streams but handle them in a much more environmentally friendly way while deriving more energy from them and even producing exciting new products.
New technology can process the same municipal trash—and now feed stock—that incinerators use into a “pellet” that can be used as “plastic wood” or a fuel supplement in large coal-burning power plants or concrete plants. This “refuse derived fuel,” or RDF, has as much as 6,000 to 8,000 BTU. (For comparison, coal has an 11,000 BTU on average.)
This new technology can pelletize residential waste/trash into RDF in a single-pass robotic processing system for up to 200 tons per day. If applied, these systems could potentially reduce the landfilling of waste by 200 times. This would greatly preserve landfill space, eliminate landfill expansions, reduce leachate issues with landfills, and prevent landfill sinkholes over time. This is an amazing technological breakthrough!
Another example is a biomass to energy system that turns food waste (the culprit for about 45 percent of landfill space) into an RDF that has about 6,000 to 7,000 BTU. These systems require only a small site, with no waste touching the facility floor and no air emissions, and can process the waste at a rate of 200 tons per day. Each load of food waste is processed in about 45 minutes and produces water that is clean enough to use for irrigation. This RDF can also augment fuels used in coal or concrete plants, with much cleaner air emissions.
Pyrolysis, gasification, and anaerobic digestion are just a few of the new biomass to energy processes that are now available for large projects, each with unique capabilities and uses. The key is targeting their advantages for each project. It is critical to partner with experienced firms who have the expertise in these specific processes and a track record of installations that are showing net positive revenue and a positive environmental impact. Many systems are being tested and designed for applications in the biomass to energy field, but clearly companies with the experience, effective financial models, history of installations, and knowledgeable operations staff are the most successful.
Exciting new applications
EBA is making in-roads into this exciting new arena by teaming with BTS Biogas, an Italian waste-to-energy (WTE) company with North American headquarters in Columbia, Maryland. BTS is constructing a WTE facility at the Maryland Food Center in Jessup, Maryland, which is home to roughly 50 merchants, food processors, and related businesses. BTS will turn food waste from these vendors into methane gas/energy using a WTE anaerobic digester that uses natural bacteria to “eat” or decompose the food waste in an oxygen-free vessel. This process will generate an ideal waste solid for use on fields for crop growth or horticultural systems.
The facility will charge a tipping fee, which is less than the local landfills charge, to pay for the project and provide operating fees. The project will handle 100 to 200 tons of food waste each day. BTS has already operated more than 150 of these systems in Europe.
On an even larger scale, Toyota plans to build a power plant in California that captures methane gas from dairy cattle manure to generate water, electricity, and hydrogen. Announced in 2017, the Tri-Gen Project at the Port of Long Beach, California, will be the world’s first commercial-scale 100 percent renewable power and hydrogen generation plant. According to Toyota, when it comes online around 2020, Tri-Gen will produce enough energy to power the equivalent of about 2,350 average-sized homes and meet the daily driving needs of nearly 1,500 vehicles—approximately 2.35 megawatts of electricity and 1.2 tons of hydrogen per day.
Everything in our world is now being examined with a more “microscopic,” sustainability-focused viewpoint, even the way we convert waste streams into energy with processes that are environmentally benign. Stay tuned for part two of this blog, which will continue to explore how cutting-edge biomass to energy technology is being applied to projects throughout Maryland.
Joseph Danquah, PE, is assistant vice president and water systems engineering department manager for EBA Engineering, Inc. He can be reached at 240.547.1127 or joseph.danquah@ebaengineering.com.